Eliminación de la pintura con plomo del metal
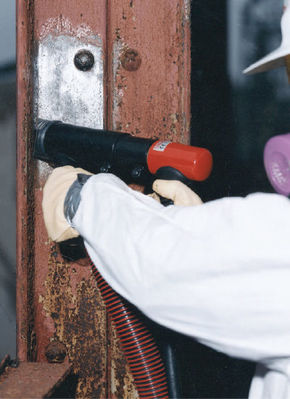
Click Here for Safety Notice
Properly removing lead paint and other contaminated coatings (such as asbestos) from steel structures can be a logistical nightmare. Contaminated particulate matter must be contained to protect the surrounding community, workers must be protected to meet OSHA standards, and hazardous waste must be properly disposed of. It can be an expensive, time-consuming endeavor.
Where Lead Coatings are Found
Lead-based paint has been banned in residential buildings since 1978, but it continues to be used as an anti-corrosion agent on iron and steel bridges, railways, ships, and other steel structures. Water, chemical, and fuel storage tanks are also commonly coated with lead paint. Contractors should assume that the protective coatings on steel structures contain lead, unless testing confirms otherwise.
OSHA Standards
Lead exposure can damage the brain and nervous system, the blood, kidneys and reproductive systems. High exposures over a short period of time or lower exposures spread out over time can cause lead poisoning. Workers on job sites where lead paint is being removed or disturbed are at risk of inhaling or ingesting lead dust, fumes or mist.
The OSHA Lead Standard for the Construction Industry[1] requires employers to implement feasible engineering and work practice controls to protect workers. Worker rotation and respirators should be utilized only as supplementary protection. Exposure can be very difficult to evaluate and control in complex construction environments where everything down to the weather can wreak havoc on even the best-laid plans.
When Does The Standard Apply?[2]
There are two key factors that determine if the lead standard applies:
- The presence of lead paint on the structure
- The scope of work includes paint disturbing activities, such as demolition, rivet busting, torch cutting, grinding, and paint removal
When these two conditions are met, there is a potential for worker exposure to lead and
The Employer Must:
- Design and implement engineering and work practice controls for each lead disturbing task before work begins.
- Begin exposure monitoring and implement interim controls if exposure results are:
- Less than 30 mcg/m3 : provide site health and safety program, wash up station, and respirators if requested.
- 30 - 49 mcg/m3 : provide blood tests, training and air monitoring.
- 50 mcg/m3 or more : implement entire standard.
Hazardous Dust & Waste Containment
As one study on worker safety highlighted[2], “rehabilitation of steel structures poses serious lead hazards not only to workers on the site, but also to nearby residents, children, and the environment.” States like Minnesota[3] have strict lead paint removal guidelines in place to protect the community surrounding potentially hazardous job sites. Physical structures are the most common means of containing particulate matter to the job site.
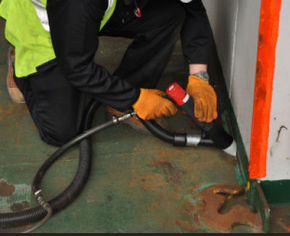
Needle Scaling vs. Blasting of Contaminated Coatings
Conventional abrasive blasting is commonly used to remove coatings from large surface areas, but the process also has serious disadvantages. Blasting generates an excessive amount of hazardous waste material that needs to be handled and disposed of properly.
Needle scalers equipped with integrated vacuum shrouds (such as the CS Unitec Trelawny TVS™ series) do an exceptional job of capturing particles containing contaminants at the source of removal when used with a HEPA dust extraction vacuum. According to one EPA study involving lead paint removal, this type of tool can reduce the airborne concentrations of respirable dusts by up to 99%[4].
As expected, additional labor is required when using needle guns rather than blasting. However, with the dust collection capabilities of these tools, workers are better protected from contaminated air compared to abrasive blasting. Money savings is realized because there is significantly less need for abrasive blast material and very costly hazardous waste disposal. The same EPA study estimated that up to 97.5% less hazardous waste was generated by shrouded needle scalers. Depending on the environment and the scope of the job, needle scalers can be a viable, cost-effective solution.
For information regarding containment structures and the use of PPE to protect workers and the surrounding environment please contact your local OSHA, EPA, State and Country regulatory offices for clarification and guidelines.
Ergonomics & Vibration
When operating power tools, workers need to be protected from excessive vibration, noise exposure, and compromised ergonomics. Low-vibration scaler models are a great solution for addressing these types of risk factors. In many cases, workers can log full shifts before hitting daily vibration exposure limits. Long-reach tools are also available to help work overhead and in other awkward, hard-to-reach areas that can lead to operator injury. With low vibration tools workers can complete a full 8-hour shift before exceeding vibration limits, reducing the need for extra personnel.
Vacuum Shrouded & Long Reach Scaling Tools | ||
Standard Needle Scalers | Low Vibration Needle Scalers | Long Reach Needle/Chisel Scaler |
Safety Notice: User is responsible for meeting all hazardous material containment requirements.Please contact your local OSHA, EPA, State and Country regulatory offices for clarification and guidelines.Further information can be found on the EPA website here. |