Finishing 304 Stainless Steel to Achieve a Uniform #4 Sanitary Appliance Finish
A pharmaceutical manufacturing facility required stainless steel enclosures to have a uniform #4 sanitary appliance finish for both aesthetic and antiseptic purposes.
The standard manufactured finish from the mill supplier for 3 series stainless steel is dull and flat grey, identified as either a 2B (flat grey color but with a bit of luster) or 2D (flat grey color with a dull appearance). When viewed alongside linear grained or polished stainless steel, the appearance is a distinct contrast. A pharmaceutical manufacturing facility noticed this finish disparity after ordering 65 stainless steel electrical enclosures from a fabricator – without specifying the desired #4 sanitary (brushed) finish in the scope of the project.
Initially, the company accepted the "unfinished" look of the 304 stainless steel enclosures, but when they were viewed alongside polished stainless vessels, piping and equipment, this finish looked very different. Though functionality was not compromised in any way, the 304 stainless enclosures contrasted dramatically with all other components in the facility.
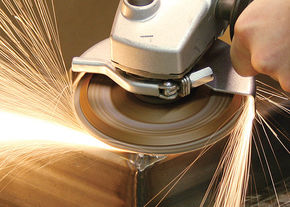
In addition, it was discovered that all the welds on the enclosures were unfinished and needed to be ground down and blended in smoothly to prevent retention of bacteria even after the routine steam cleaning process.
After relaying these issues to the fabricator making the electrical enclosures, a #4 sanitary (brushed) finish was agreed upon for the welded boxes already delivered and those yet to be manufactured, with welds seams and corners blended in for uniformity and to ensure passivation of the surface.
To achieve the desired finish, the fabricator contacted CS Unitec for the solution.
Step One:
The Technical Support Application Engineers from CS Unitec recommended a two-part process to achieve the desired finish. The first step was using the CS Unitec Varilex WSF 1800 (65000A) variable-speed right angle polisher and the new Plantex Ceramic Sunfire 5-inch 60 grit easy-mount flap disc to blend in the weld seams and prepare the enclosures for finishing. This disc blends the weld like a 60-grit disc but leaves the finish of an 80-grit disc, making it easier to produce a uniform final finish. In addition, the Sunfire disc has a grinding aid incorporated into the flaps to allow the disc to run cooler, preventing the overheating of the work surface. After blending in all the welds with the Sunfire disc, the enclosures moved on to final finishing.
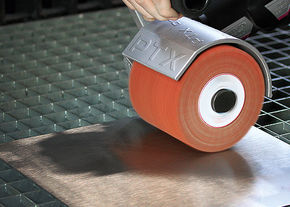
Step Two:
To produce the #4 sanitary brushed linear finish, the engineers at CS Unitec recommended the PTX Linear polisher (47002). This multi-functional blending and polishing tool features a 15-amp motor that delivers constant power to the spindle and is equipped with a variable speed function to achieve or match nearly any finish.
The following process was recommended to produce the #4 sanitary appliance finish.
1. Pre-grinding - Pre-grind with PTX flap wheel 47212 (60grit), 47213 (80 grit) to create the desired straight-line scratch pattern.
2. Final Grinding/Industrial Finish - Final finish with PTX fleece (nonwoven) wheel 47412 (80 grit) or Interleaf (combi) wheel 47312 (80 grit). This produces a straight-line finish corresponding to a #4 sanitary brush finish with a grain standard of 150‐180 grit.
Conclusion
The combination of the Varilex WSF 1800 rotary tool equipped with the Sunfire disc and the PTX Eco Smart polisher using the flap wheel to set the scratch and the fleece wheel to soften the scratch pattern was the ideal solution to this application and both the fabricator and the end user are satisfied with the results.