Stainless Steel Metal Polishing Guide
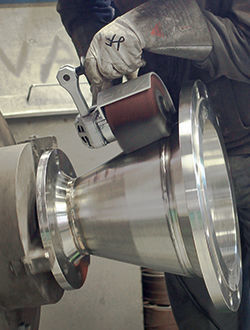
With the PTX ECO SMART and the below guide you can accomplishing anywhere from a matte to a mirror finish and many phases in between.
The PTX ECO SMART linear finishing machine can be used to blend welds, remove scratches and replicate almost any factory finish back to the original state.
To match a # 4 appliance finish that corresponds to the grain standard 150/180 grit, we recommend the following operations:
- Removal of scratches with the PTX sanding flap wheel:
- 40 grit (P/N 47211) or 60 grit (P/N 47212)
- Blend the area with the PTX Fleece non-woven wheel 80 grit (P/N 47412)
To match a #6 satin finish that corresponds to the grain standard 240 grit, we recommend replacing step 2 above and instead:
- Blend the area with the PTX fleece non-woven wheel, 180 grit (P/N 47413)
To create a #7 finish:
- The stainless steel can be worked with the PTX Gum Wheel. This is a soft rubber polishing wheel made of rubber compound interspersed with abrasive, 60 grit (P/N 45061).180 grit (P/N 45181).
To create a #8 finish:
- Start with the TZ pyramid belts on the expansion roller (P/N 47005) and use the following TZ Belt Grits in order, 220 grit (P/N 42270), followed by 280 grit (P/N 42265), 400 grit (P/N 42245), 600 grit (P/N 42230), 1200 grit (P/N 42216), 2000 grit (P/N 42206).
- With each change of grit, the operator changes the presentation by 90 degrees, to reduce the scratch into smaller pieces that can be removed by the next grit size.
- After all scratches are removed use the white polishing paste (P/N 40013) then blue polishing paste (P/N 40014) polishing compound with the PTX felt sleeve (P/N 42013). Ensure that different felt sleeves are used for each level of polishing compound. The polishing process should be completed in all directions.
- Use the Brightex soft, clean powder (P/N 40028 or 40029) between each step of compound to remove excess compound from the surface.
- Last finish with polishing cream (P/N 40015) on a cotton buffing wheel (P/N CS2410) in one direction only with little or no pressure to achieve the desired luster.
Due to differences in stainless steel (VA – metal). This application guide is only a suggested method and a fabricator will need to test how they can obtain the required final finish in the best way.
For further tips and technical advice regarding stainless steel metal polishing please call to talk to our surface finishing experts 1-800-700-5919 or 203-853-9522.
Do you have round surfaces to polish?
Try the PTX ECO SMART with our open and closed loop belts.
Or for more regular use, upgrade to the PIPE-MAX pipe polishing machine. All of the same abrasive grits in the above guides can also be found for the PIPE-MAX here.
Do you have rotary metal polishing needs?
The VARILEX rotary polishing machine can be a versatile tool for rotary finishing. All of the same abrasive grits in the above guides can also be found for the VARILEX here.
Tips for stainless steel metal polishing:
Now armed with all of this technical guides for stainless steel metal polishing, the next question is, “What can go wrong?”
The customer’s expectations are crucial. Finishes that are simple, such as a grain that runs the length of a rail, have a lower time-cost factor than a difficult finish, such as a grain that goes around the circumference of a square tube or pipe.
Before assembly, ensure that all pre-grained pieces have a consistent pattern. When welding two or more pieces together, make sure the grain lines are aligned and in the same direction. A mistake early in the process is impossible to correct.
Always choose the correct application-specific tool for the project. This will increase productivity and decrease total costs.
Use “Start at the finish” as a guiding principle. Never put any scratches into a workpiece that you will need to remove later to achieve a desired finish.
Haste makes waste. The best finish is achieved with time and patience. Cutting corners by using abrasive grits that are too aggressive, applying too much pressure, or using tools at incorrect speeds often results in increased cost, decreased productivity, and failure to achieve the required finish.
Want to read more about stainless steel metal finishing? Check out these articles below.
How to Get a Mirror Finish on Stainless Steel
Finishing 304 Stainless Steel to Achieve a Uniform #4 Sanitary Appliance Finish
How to Get Industrial Straight Line Finish on Stainless Steel
Finishing Stainless Steel for Food Grade Applications